
I've done all that in the template files so all new part files have the required fields. That being said, you do need to make sure to edit your parameters for each part to insure your material (also entered as a user parameter) is correct. Works great with part files, not so great with assembly files. The key was creating a user parameter for cost, then writing a little iLogic code to take that information and place it into the iProperties "Estimated Cost" field.
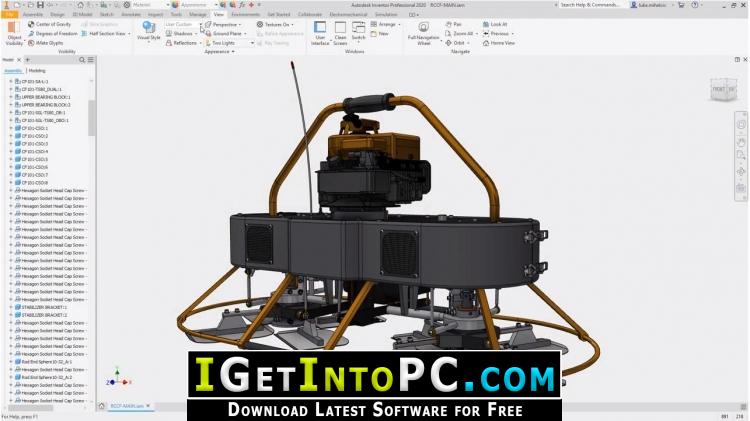
That being said, with help from this forum, I finally got some functionality with that particular iProperties field. I did finally get a handle on some basics of iLogic programming with plenty of help from this forum. since I originally started this thread, I feel the need to update what I've done. Here's a link that gives a basic example of doing this with Inventor and iLogic:īest of luck to you in all of your Inventor pursuits, During that time I generated takes offs using an Excel price list that was updated when needed, and even that was not ideal, we just didn't have the ability to tie directly into the ERP at that time. Many years back when China was buying all of the steel it could get to build the Three Gorges Dam, our material costs fluctuated quite a bit for many months.
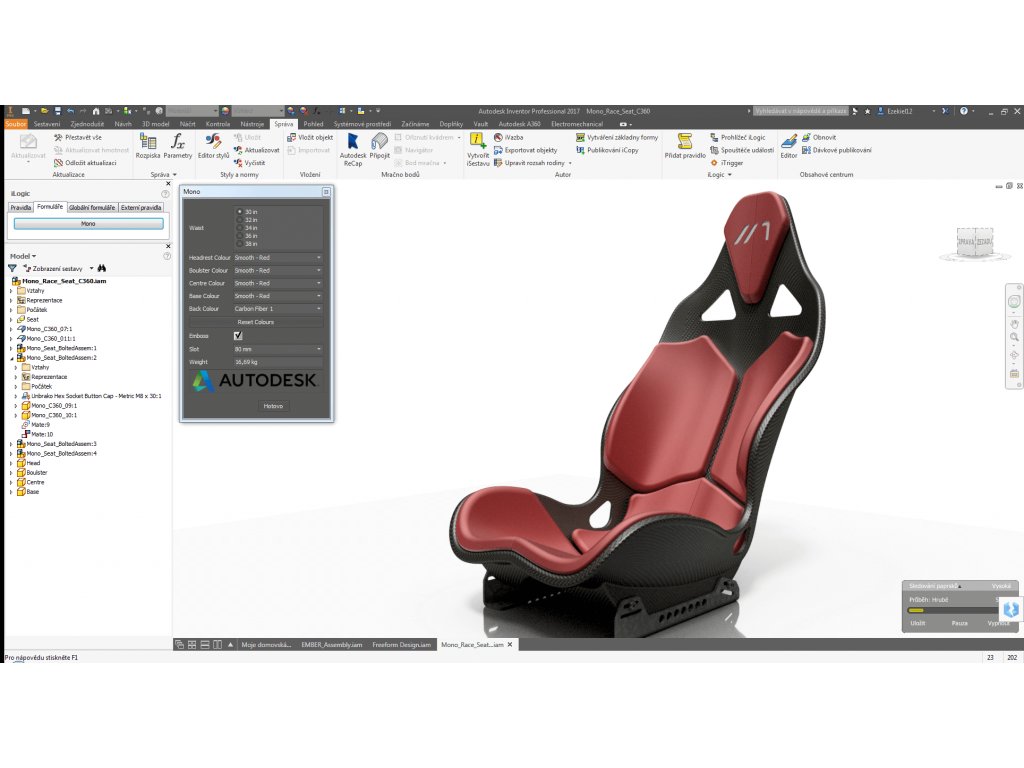
It worked well, and if the pricing changed, it could be updated in one Excel file rather than hundreds of CAD files.
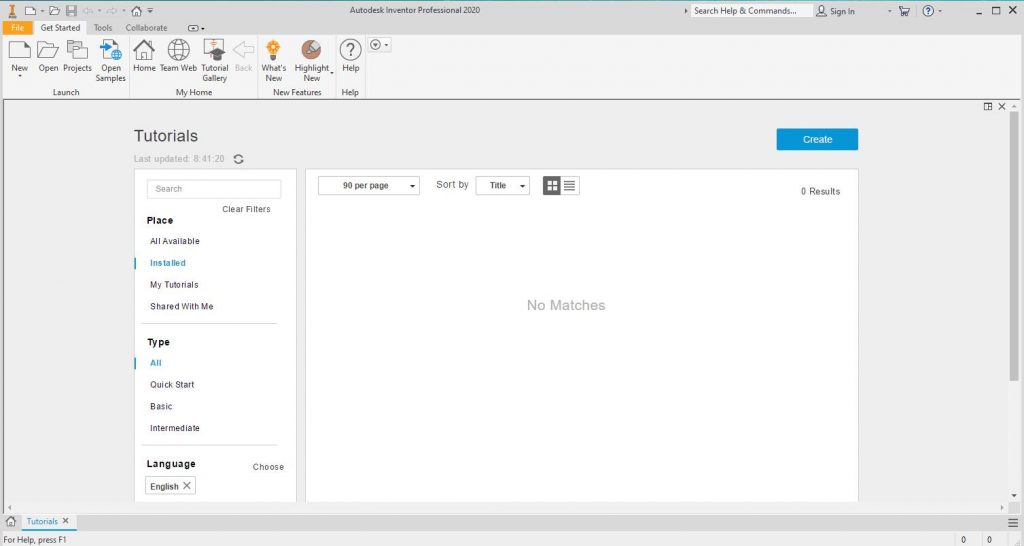
I've used the workflow of exporting the BOM / Parts list to an Excel template that housed the pricing info a lot it the past, when I used to have to generate take offs. I've always felt that putting pricing into CAD files was not the best idea, and could be better managed in Excel.
